Analysis of the Adaptability of Ink to High-speed Roll Concave
Abstract: This article starts with the requirements of high-speed gravure printing inks, and expounds on the solvent, wax, pigments, fillers, dispersants, resins, etc., and makes a simple analysis and discussion on the ink's adaptability.
Keywords: high speed, film formation, ink head, adjustment
The printing industry is undergoing development from quantitative to qualitative change. The speed of current gravure printing presses has reached 250-350 m/min, and even faster, and very high performance requirements have been put forward for the inks.
We know that in the normal printing process, due to the fact that the resin in the final stage of the film-forming process tends to be too long due to the ink head, slowing down the drying time, that is, blocking the normal rapid release of the solvent, will directly affect the The speed of packaging and printing, the quality of the pros and cons. The direct influence is the ef- fectiveness of packaging and printing, the production cost, and the initial adhesion performance of the substrate. In the actual operation process, the adhesion performance can be judged by whether the ink film can be detached by sticky tape. Occasionally, the occurrence of such pull-off failures often causes ink printers to take great pains.
How to measure the value of the product from the perspective of ink performance, to change the quality of printed products, which is the main issue discussed in this article, there are improper points please a lot of experts and scholars.
First, the solvent
It is the most intuitive method to adjust the ink when speeding up the printing speed and increase the proportion of solvent, preferably the proportion of quick-drying solvent. However, in the printing process, due to the performance limitations of the original ink, it is impossible to make a wide range of adjustments. In addition, the intuitive point is that it often leads to an increase in the cost of thinners, especially when oil is greatly increased.
Before increasing the solvent, it is necessary to consider whether the color density of the ink becomes shallow, that is, the viscosity of the packaging printing ink is not the same under the same solvent conditions. For example, after adding 30% of the solvent, consider its solubility, hydrogen bonding force, volatilization rate balance, surface tension and so on. Generally speaking, from the solvent ratio, the following three recipes have their own merits:
Formula 1: Xylene 9.6 Butyl acetate 9 Ethyl acetate 26.4 Toluene 55
(its properties are: volatile rate 2.94; solubility 8.98; hydrogen bonding force 18.18; surface tension 26.9; molecular weight 90.55)
Formula 2: Toluene 70 Ethyl Acetate 30
(its nature is: Volatile rate 2.94; Solubility 8.98; Hydrogen bonding force 18.12; Surface tension 27.1; Molecular weight 90.86)
Formula 3: Toluene 73.3 Ethyl Ketone 26.7
(its properties are: volatility rate 2.94; solubility degree 9.05; hydrogen bond strength 18.18; surface tension 27.09; molecular weight 84.72)
A brief analysis from the above three recipes:
1. Viscosity: Formula 2 has a high viscosity, Formula 1 has a moderate viscosity, and Formula 3 has the lowest viscosity.
2. Drying speed from two solvents alone: ​​1 and 2 and 3 drying speeds look the same, but there are still differences. Formulations 1 and 3 have the same volatilization rate, but 3 has a low viscosity and relatively low volatility drying.
3, from the cost comparison, 3 to 1 cost slightly higher. But the susceptibility and attachment of 3-butanone remained slightly worse than 1.
4. Compared with comprehensive benefits, formula 2 has low cost, high viscosity, good adhesion, low odor and better solubility. However, in the actual package printing process, the solvent volatilization balance at the time of film formation of the ink is better than that of Formulation 1, which is better than 2, 3, since many solvents have the same volatilization rate in terms of conversion, but due to a variety of ) Solvent dilutes the ink to improve the range of printability of the package printing, allowing the printing manufacturer to have a broader range of solvent selection and printing machine speed adjustment surfaces.
Because of the evaporation of a single solvent during the process of independent packaging printing, it is dried by the slow evaporation (the process of film formation of printing ink). When the wet ink film of its printing ink reaches a certain interface strength, it will solidify into a film. The process of forming the ink film for printing and printing also reduces the solvent of the printing ink film that has been volatilized (ran away) in the future, and prolongs the thorough drying time (dryness) of the ink film for packaging and printing. As a result, a phenomenon (failure) occurs after the tape is peeled off from the tape after printing.
For this reason, a general printing operator selects a solvent-dilution ink having a small molecular weight (ie, a small viscosity) and a fast film formation for the printing job, and a low-molecular-weight solvent is an overhand method for cutting the silk head of the printing ink.
Second, the use of wax additives
The purpose of adding wax or enlarging wax is to reduce the above-mentioned consequences caused by the long thread head during the printing process of the ink, and secondly, to solve the problem of the ink system's color, filler agglomeration and ink film hardness, and can effectively improve The ink film thickness during the packaging printing process. However, too much addition tends to hinder the volatilization of the solvent in the printing ink system, thorough drying and surface crusting, and ink transfer, poor flowability in the transfer printing process, reduction in surface gloss, and the like.
Therefore, it is very effective in solving the problems of package printing, blocking, blocking, and masking. However, the excessive addition will speed up the softening of the ink film, causing the printing transfer rubbing ink to heat up and causing the ink splash to malfunction.
Third, increase the proportion of pigments and fillers
The increase in solid color and filler is a very simple method for reducing the film formation of packaging printing inks. Its role is to disperse the coating ratio of the resin (competitive adsorption) to prevent the filament from becoming too long. The ultimate goal is to prevent the printing machinery from advancing from slow to fast. The thinning of the film is thickened; trailing and eliminating the edge ghost due to the flow of the ink; the ink is remedied due to poor hiding power.
Fourth, increase the proportion of organic dispersants
Its function is to reduce the shortening of the ink head (viscosity) required for printing due to shearing of the agitated, abraded ink during the ink-making or printing process. However, excessive plasticization (as far as possible not to choose dispersants of plasticizers) dispersants often results in a decrease in the adhesion fastness of composite printing inks and composite glues, or compounding and dry compounding.
Generally, TM-3 is added into Tianyang Chemical Factory at the time of ink manufacture or at the time of printing. This not only prevents the resin from being excessively swelled under the influence of the solvent, but also limits the unrestrained stretching of the resin solution's filament head (because the polymer resin When pulled by an external force, curl-stabilized molecules will gradually elongate and stretch. However, as a printer can be added temporarily when using it, do not add plasticizer because it is long, otherwise it will stretch the filament again.
Fifth, adding emulsifiers
The easiest way is to add bentonite or white carbon black. After being sufficiently stirred and dispersed, hydrogen bonds are formed between the silanol groups, resulting in a bulky network structure and thickening of the ink film. The latter tends to cause the ink to swell due to its intervention. When the solvent is added to dilute the printing, the hue of the general printing image becomes lighter due to hairiness.
Six, the choice of resin or mixed skills
Whether it is glue, lead, screen printing, or gravure printing ink in the surface or inside, it is better to select the resin linking material corresponding to the printing machine speed as soon as possible, that is, the faster the speed, the lower the viscosity of the resin and the shorter the wire head. For example, the binder (ie, resin) of the gravure composite printing ink system is formulated with a formula that matches the high chlorine content of CPP or CEVA.
First, the higher the chlorine content, the easier it is to disperse, the lower the viscosity and the shorter the filament head. However, when the packaging ink and the substrate are compounded, the attachment fastness of the ink and the substrate is often directly related. Because the filament of the high-chlorine content resin is short, the crystallization phenomenon of the ink during the printing process is gone. The possibility is also small, the viscosity is low, but the composite fastness is reduced, the stability of the ink in the storage process is also reduced (such as the occurrence of precipitation, foam, etc.), the printed graphics floating color printing process and many more.
Secondly, in order to solve the above problems, usually more than two types of resin inks are used or inks are added during the printing process to overcome them. The one with low viscosity is selected as a tackifier or the chlorine content of the same kind is selected to be small or Low molecular weight (low viscosity) resins are commonly used methods. The purpose of adding silicone oils or dispersants is nothing more than a passive remedy that is based on low filament length or low color concentration. For example, increasing the lower molecular weight MP-45 or CEVA to EVA, etc., although the silk head problem, frost resistance problem, dispersion problems, and adhesion problems have all been improved, the cost of the packaging printing ink has increased significantly. However, if you do not pay much attention, the softening point of the resin in the ink system will be reduced. This will result in sticking due to defects in the printing process during the hot season, or printing in the winter at low temperatures, and will still cause problems in packaging during the hot season. After the stockpiling, the reprinting of the printed graphic is re-plasticized (softened) and scrapping occurs again.
Thirdly, due to the excessive length of the wire head, although it is well attached, the surface of the substrate is too difficult to be classified and transported due to the graphic ink film of the packaging printing ink, which is a common saying called smoothness. In fact, when the softening point of the resin is lower than 104°C, blocking or rebonding of the printed product occurs when the room temperature reaches or exceeds 35°C. This refers to packaging printing inks produced from thermoplastic resins, while thermosetting inks present one or more problems during the printing process (such as deformation, splashing of printed ink, etc.). It is very important to increase or pay attention to the selection, grafting, and collocation of resins in packaging printing ink systems. Secondly, it is the only way to completely avoid the above-mentioned failures by seriously treating the detection of viscosity and softening points or comparing them with tests. Very important and necessary.
Source: China Infinity
This rising Tv Lift is intended to keep your television out of site, either behind a console or bureau, or just in its lowered state. It can also be installed behind fireplace mantles, sideboards, credenzas, and nearly anywhere else. This sturdy TV lift can lift up to 39" from a fully lowered position (at 0.98"/second). All of this is controlled by a convenient wireless RF remote control.
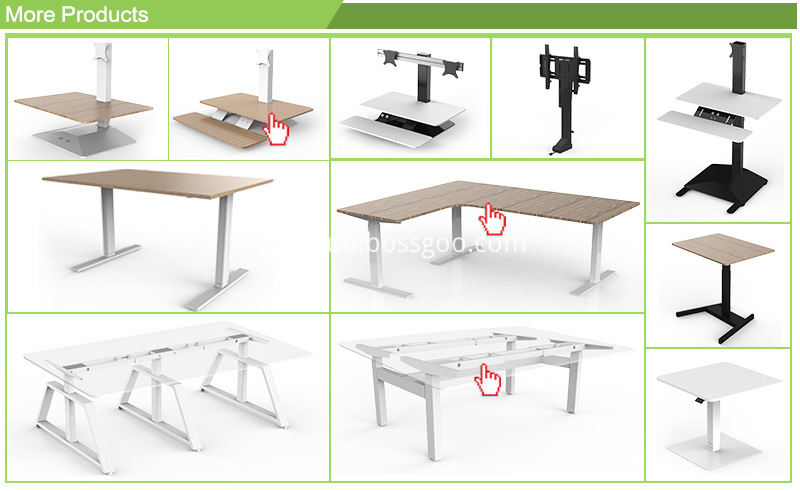
Motorized TV Lift
Motorized Tv Lift,Desk Tv Lift,Motorized Lcd Tv Lift,Motorized Mobile Tv Lift
Shaoxing contuo Transmission Technology Co.,Ltd , http://www.electricdesk.nl