New green honeycomb paperboard and pulp molding technology and application
2021-10-28 16:04:56
Introduction: In today's world, environmental protection is one of the key issues for human survival in development. The problem of environmental pollution and waste of resources brought about by packaging has attracted the attention of countries all over the world. Therefore, green packaging has undoubtedly become the mainstream development direction of international packaging.
At present, the EU countries have strict restrictions and regulations on wooden pallets, wooden crates, EPS foam plastics, adhesives, printing inks, coatings and other packaging materials, accessories and their packaging waste, which constitutes the export of China's goods. Direct obstacles. Therefore, as a new type of green paper packaging, honeycomb paperboard and pulp molding can meet the requirements of saving resources, protecting the ecological environment, and conforming to the international packaging development trend.
Honeycomb Cardboard Honeycomb Cardboard Overview Honeycomb paperboard is made according to the structural principle of the natural honeycomb. It uses recycled paper to form a number of uniformly distributed hexagonal day-dyed honeycombs, and then successively bonds the recycled paper of different energy materials to a new environmentally friendly material after drying and solidification.
The structure of the honeycomb paperboard is a two-layer paper with upper and lower layers, and a honeycomb core paper in the middle, which is bonded into a three-layer structure by an adhesive. The thickness variation of the honeycomb paperboard is mainly realized by changing the thickness of the honeycomb core paper, and the thickness thereof generally varies between 5 mm and 90 mm, and the column hole size of the honeycomb paper core can also be changed according to the required strength.
Honeycomb paperboard can meet the packaging needs of electronic and electrical appliances because of its wide application, high strength, large bearing capacity, good elasticity, saving raw materials, low cost, small quality and recyclability. It is especially suitable for heavier appliances and electromechanical. Buffer packaging for industrial products such as products and ceramics. Honeycomb paperboard can be made into honeycomb trays, crates and packaging liners. At the same time, the honeycomb paperboard is combined with other materials to form a new honeycomb composite. Honeycomb composite material is a new type of material with light weight, high strength and high rigidity. It has functions of cushioning, vibration isolation, heat preservation, heat insulation and sound insulation. It is widely used in construction industry, furniture manufacturing, packaging and transportation. Industry, replacing wood, clay bricks and high-expanded polystyrene, has high economic value; at the same time, it can be recycled, saves a lot of forest resources, protects and improves the ecological environment, and is a new type of green packaging material that meets environmental protection requirements.
Application of Honeycomb Paperboard in Packaging Honeycomb Paperboard Packaging Box Honeycomb paper core of the honeycomb cardboard packaging box is respectively bonded with different gram weight paper sheets to make various forms and specifications of packaging boxes. This type of container is an ideal container for fragile, fragile, and commodity packaging, and can be used as an alternative to corrugated boxes.
Honeycomb cardboard lining packaging box This kind of packaging box adopts honeycomb paperboard with better cushioning performance on the inner side of the original corrugated cardboard box, which can enhance the shockproof, anti-pressure and anti-puncture ability of the corrugated box, and is more suitable for electronic products and glassware. Packaging of valuables such as blood, instrumentation, and medical equipment.
Honeycomb Cardboard Tray The trays and paving of the trays are made of cured honeycomb paperboard, which is inexpensive and easy to recycle, suitable for storage and single use.
The honeycomb paperboard composite tray honeycomb paperboard composite tray is made of honeycomb paper core and fiberboard composite. The paving beam is made of wooden beams or fixed composite core strips, and the frame is fixed by wooden strips. This type of pallet has a large bearing capacity and can be reused. It can replace wooden pallets and steel flat pallets within a certain range. The cost is only 1/3 of that of steel pallets. After use, it can save money and achieve better economic benefits.
Honeycomb composite panels are used in furniture manufacturing on furniture, and honeycomb composites are mostly used in the form of honeycomb composite panels. The honeycomb composite board is a composite board formed by sizing and pressure bonding a thin artificial board and a honeycomb paper core. As a sandwich material, the honeycomb paper core material accounts for only about 1% to 5% of the solid material, and the use of 1 ton of honeycomb paper composite material can replace 30 to 50 cubic meters of wood.
Since honeycomb composite materials replace wood in the manufacture of furniture, the use of wood is greatly reduced, and therefore, it is widely promoted and used in the furniture manufacturing industry, and can effectively improve the defects of the deformation of the artificial board. Taking a 20 mm thick plate as an example, if a 2.5 mm MDF is used as a panel to make a honeycomb composite panel, the amount and weight of the material is only about 1/4 of that of the solid MDF; and the cost of the composite panel is only solid. The board is about 1/2, and the composite board has the advantages of light weight, non-deformation, and convenient transportation. Thus, in Europe, more than 80% of interior doors are honeycomb composite doors, and most furniture sheets above 20 mm thickness are honeycomb composite panels. Honeycomb composite panels are ideal for use in panel furniture. For example, it can be used for panels, top panels, partitions, floor panels, door panels and some decorative pieces having a thickness greater than 18 mm. The thicker the plate, the more superior the honeycomb material is; the thick plate also has good bending resistance for the dining table, coffee table, TV cabinet and so on. There are even furniture manufacturers who use it to make support legs for furniture, which shows the wide range of applications.
Pulp Molding Pulp Molding Overview Pulp Molding is a three-dimensional papermaking technology. It refers to a certain concentration of pulp added with an appropriate amount of chemical additives. In the molding machine, the fibers are evenly distributed on the surface of the mold by vacuum or pressure, thereby making a wet paper. The mold blank is further dehydrated and demolded, and the product is dried and shaped to produce a pulp molding product. Products made from waste paper of different compositions have different properties. Therefore, according to the use of the product, different waste paper or several kinds of waste paper can be used together to obtain better economic benefits and performance. Pulp molded articles can be designed to improve their structure, and materials or surfaces which are added to various ingredients at the time of manufacture are specially treated to achieve the desired properties and characteristics for an article or a certain condition. In addition, the characteristics of the paper mold obtained by using different processing methods are different, so changing the processing method or process can improve the performance of the paper mold.
Pulp Molding Production Process The industrial packaging pulp molding production equipment and structure are substantially the same as the pulp molded tableware. The mold is used for vacuum adsorption forming, drying, and deep processing to make finer products. The production line is generally composed of two parts: forming equipment and drying equipment. The tableware products are also required to increase the integral calendering and disinfection and sterilization due to their higher requirements. The paper forming method is roughly divided into two types: external vacuum forming and in-mold grouting. The drying method is divided into two types depending on the forming method. The external vacuum adsorption molding usually adopts the external drying method, and the in-mold grouting extrusion is mostly directly heated and dried in the mold.
At the current state of the art, the thickness of the paper molded product is generally between 1 mm and 60 mm, and the thickness of the general product is kept at about 2.5 mm; from the current quality and application of the paper molded product, the large load bearing capacity Up to 200kg, the shape is not too complicated, and the product lining packaging with weight less than 50kg is a good choice; the cushioning effect of the paper mold packaging is mainly achieved by the elastic deformation of the paper wall when it is impacted, thereby slowing down the external force. . The elasticity of the paper mold material itself is not high, mainly depends on the support rib design of the product and the buffering cavity formed by the product. The design of the support rib plays a vital role in the elastic deformation of the paper mold packaging product, that is, the buffering ability. The basic basis for the design of the support ribs is the shape and use of the product itself.
Compared with disposable expanded polystyrene products, pulp molded products have abundant raw materials, no pollution during production and use, light weight, high compressive strength, good cushioning performance and good recyclability. Sex, so it is widely used in packaging. Its application range includes food containers, beverage cup holders, medical equipment, cosmetics, fruit trays, mechanical parts, hardware tools, furniture accessories, handicrafts, electronic products, electrical appliances, communication equipment and audio equipment. However, the pulp molded product is easily deformed after being wet, and the strength is decreased; if the product is not specially treated, the appearance is lower.
The "4R 1D" principle, that is, low-consumption, recyclable, re-usable, recycled and degradable green packaging, can better achieve the coordinated development between packaging and environmental protection and resource regeneration. Honeycomb paperboard and pulp molding, as two new types of green packaging technology, have achieved rapid development in today's packaging industry with their superior performance. At the same time, the new green paper packaging is in international trade and meets the requirements of the developed countries for the environmental performance of packaging. Therefore, the development of green packaging is in line with the trend of world packaging development, is conducive to breaking through the international green trade barriers, and is also conducive to the harmonious integration of packaging in its function and environmental protection.
At present, the EU countries have strict restrictions and regulations on wooden pallets, wooden crates, EPS foam plastics, adhesives, printing inks, coatings and other packaging materials, accessories and their packaging waste, which constitutes the export of China's goods. Direct obstacles. Therefore, as a new type of green paper packaging, honeycomb paperboard and pulp molding can meet the requirements of saving resources, protecting the ecological environment, and conforming to the international packaging development trend.
Honeycomb Cardboard Honeycomb Cardboard Overview Honeycomb paperboard is made according to the structural principle of the natural honeycomb. It uses recycled paper to form a number of uniformly distributed hexagonal day-dyed honeycombs, and then successively bonds the recycled paper of different energy materials to a new environmentally friendly material after drying and solidification.
The structure of the honeycomb paperboard is a two-layer paper with upper and lower layers, and a honeycomb core paper in the middle, which is bonded into a three-layer structure by an adhesive. The thickness variation of the honeycomb paperboard is mainly realized by changing the thickness of the honeycomb core paper, and the thickness thereof generally varies between 5 mm and 90 mm, and the column hole size of the honeycomb paper core can also be changed according to the required strength.
Honeycomb paperboard can meet the packaging needs of electronic and electrical appliances because of its wide application, high strength, large bearing capacity, good elasticity, saving raw materials, low cost, small quality and recyclability. It is especially suitable for heavier appliances and electromechanical. Buffer packaging for industrial products such as products and ceramics. Honeycomb paperboard can be made into honeycomb trays, crates and packaging liners. At the same time, the honeycomb paperboard is combined with other materials to form a new honeycomb composite. Honeycomb composite material is a new type of material with light weight, high strength and high rigidity. It has functions of cushioning, vibration isolation, heat preservation, heat insulation and sound insulation. It is widely used in construction industry, furniture manufacturing, packaging and transportation. Industry, replacing wood, clay bricks and high-expanded polystyrene, has high economic value; at the same time, it can be recycled, saves a lot of forest resources, protects and improves the ecological environment, and is a new type of green packaging material that meets environmental protection requirements.
Application of Honeycomb Paperboard in Packaging Honeycomb Paperboard Packaging Box Honeycomb paper core of the honeycomb cardboard packaging box is respectively bonded with different gram weight paper sheets to make various forms and specifications of packaging boxes. This type of container is an ideal container for fragile, fragile, and commodity packaging, and can be used as an alternative to corrugated boxes.
Honeycomb cardboard lining packaging box This kind of packaging box adopts honeycomb paperboard with better cushioning performance on the inner side of the original corrugated cardboard box, which can enhance the shockproof, anti-pressure and anti-puncture ability of the corrugated box, and is more suitable for electronic products and glassware. Packaging of valuables such as blood, instrumentation, and medical equipment.
Honeycomb Cardboard Tray The trays and paving of the trays are made of cured honeycomb paperboard, which is inexpensive and easy to recycle, suitable for storage and single use.
The honeycomb paperboard composite tray honeycomb paperboard composite tray is made of honeycomb paper core and fiberboard composite. The paving beam is made of wooden beams or fixed composite core strips, and the frame is fixed by wooden strips. This type of pallet has a large bearing capacity and can be reused. It can replace wooden pallets and steel flat pallets within a certain range. The cost is only 1/3 of that of steel pallets. After use, it can save money and achieve better economic benefits.
Honeycomb composite panels are used in furniture manufacturing on furniture, and honeycomb composites are mostly used in the form of honeycomb composite panels. The honeycomb composite board is a composite board formed by sizing and pressure bonding a thin artificial board and a honeycomb paper core. As a sandwich material, the honeycomb paper core material accounts for only about 1% to 5% of the solid material, and the use of 1 ton of honeycomb paper composite material can replace 30 to 50 cubic meters of wood.
Since honeycomb composite materials replace wood in the manufacture of furniture, the use of wood is greatly reduced, and therefore, it is widely promoted and used in the furniture manufacturing industry, and can effectively improve the defects of the deformation of the artificial board. Taking a 20 mm thick plate as an example, if a 2.5 mm MDF is used as a panel to make a honeycomb composite panel, the amount and weight of the material is only about 1/4 of that of the solid MDF; and the cost of the composite panel is only solid. The board is about 1/2, and the composite board has the advantages of light weight, non-deformation, and convenient transportation. Thus, in Europe, more than 80% of interior doors are honeycomb composite doors, and most furniture sheets above 20 mm thickness are honeycomb composite panels. Honeycomb composite panels are ideal for use in panel furniture. For example, it can be used for panels, top panels, partitions, floor panels, door panels and some decorative pieces having a thickness greater than 18 mm. The thicker the plate, the more superior the honeycomb material is; the thick plate also has good bending resistance for the dining table, coffee table, TV cabinet and so on. There are even furniture manufacturers who use it to make support legs for furniture, which shows the wide range of applications.
Pulp Molding Pulp Molding Overview Pulp Molding is a three-dimensional papermaking technology. It refers to a certain concentration of pulp added with an appropriate amount of chemical additives. In the molding machine, the fibers are evenly distributed on the surface of the mold by vacuum or pressure, thereby making a wet paper. The mold blank is further dehydrated and demolded, and the product is dried and shaped to produce a pulp molding product. Products made from waste paper of different compositions have different properties. Therefore, according to the use of the product, different waste paper or several kinds of waste paper can be used together to obtain better economic benefits and performance. Pulp molded articles can be designed to improve their structure, and materials or surfaces which are added to various ingredients at the time of manufacture are specially treated to achieve the desired properties and characteristics for an article or a certain condition. In addition, the characteristics of the paper mold obtained by using different processing methods are different, so changing the processing method or process can improve the performance of the paper mold.
Pulp Molding Production Process The industrial packaging pulp molding production equipment and structure are substantially the same as the pulp molded tableware. The mold is used for vacuum adsorption forming, drying, and deep processing to make finer products. The production line is generally composed of two parts: forming equipment and drying equipment. The tableware products are also required to increase the integral calendering and disinfection and sterilization due to their higher requirements. The paper forming method is roughly divided into two types: external vacuum forming and in-mold grouting. The drying method is divided into two types depending on the forming method. The external vacuum adsorption molding usually adopts the external drying method, and the in-mold grouting extrusion is mostly directly heated and dried in the mold.
At the current state of the art, the thickness of the paper molded product is generally between 1 mm and 60 mm, and the thickness of the general product is kept at about 2.5 mm; from the current quality and application of the paper molded product, the large load bearing capacity Up to 200kg, the shape is not too complicated, and the product lining packaging with weight less than 50kg is a good choice; the cushioning effect of the paper mold packaging is mainly achieved by the elastic deformation of the paper wall when it is impacted, thereby slowing down the external force. . The elasticity of the paper mold material itself is not high, mainly depends on the support rib design of the product and the buffering cavity formed by the product. The design of the support rib plays a vital role in the elastic deformation of the paper mold packaging product, that is, the buffering ability. The basic basis for the design of the support ribs is the shape and use of the product itself.
Compared with disposable expanded polystyrene products, pulp molded products have abundant raw materials, no pollution during production and use, light weight, high compressive strength, good cushioning performance and good recyclability. Sex, so it is widely used in packaging. Its application range includes food containers, beverage cup holders, medical equipment, cosmetics, fruit trays, mechanical parts, hardware tools, furniture accessories, handicrafts, electronic products, electrical appliances, communication equipment and audio equipment. However, the pulp molded product is easily deformed after being wet, and the strength is decreased; if the product is not specially treated, the appearance is lower.
The "4R 1D" principle, that is, low-consumption, recyclable, re-usable, recycled and degradable green packaging, can better achieve the coordinated development between packaging and environmental protection and resource regeneration. Honeycomb paperboard and pulp molding, as two new types of green packaging technology, have achieved rapid development in today's packaging industry with their superior performance. At the same time, the new green paper packaging is in international trade and meets the requirements of the developed countries for the environmental performance of packaging. Therefore, the development of green packaging is in line with the trend of world packaging development, is conducive to breaking through the international green trade barriers, and is also conducive to the harmonious integration of packaging in its function and environmental protection.
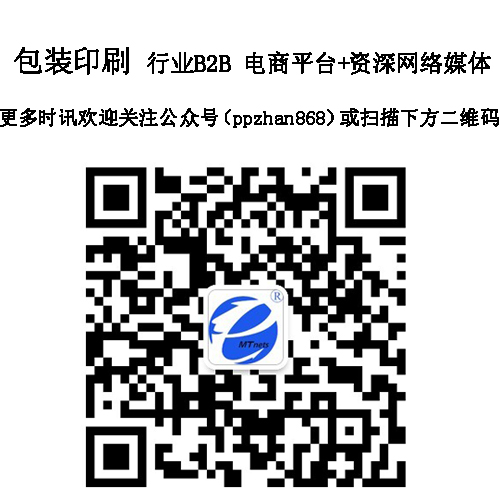
Elevator Oil Buffer
- elevator hydraulic buffer
- elevator oil buffer
- Elevator Oil Buffer with inside spring
- Elevator Hydraulic Oil Buffer
-
Elevator polyurethane buffer
Product
- Elevator Oil Buffer, Safety Device , Rated Speed up to 2.5m/s
- Elevator Oil Buffer, Free State Height 780mm 0BD220
- Hydraulic Elevator Oil Buffer With Inside Spring, 0.25m/s - 1.0m/s OB10
- Elevator Oil Buffer, 900Kg - 2500 Kg Elevator Polyurethane Buffer , 0BA70
- Hydraulic Elevator Oil Buffer,100-860mm Plunger Stroke
Elevator Oil Buffer, Hydraulic Elevator Oil Buffer
Ningbo Xinda Elevator Traction Technology Co., Ltd. , https://www.xinda-elevator.com