Improve printing quality by controlling screen plate tension
Abstract : The importance of tension control for screen printing plates, and the relationship between plate tension and screen spacing are introduced. Afterwards, we discussed in detail the various print quality problems caused by insufficient plate tension. Finally, it summarizes how to adjust the tension of the plate from various stages such as prepress preparation to printing, so as to obtain the best print.
Keywords: Screen printing; Plate tension; Net pitch
Screen printing can be carried out on almost any material, especially on some decorative advertising materials, and has a dominant position in the field of decorative printing. The printed image has a thick ink layer and bright colors, while the low printing cost is unmatched by other printing methods. As we all know, due to the limitations of the screen printing process itself, its dot reproduction capability is poor, and it is difficult to obtain perfect image details, which is one of its biggest drawbacks. Moreover, due to subjective factors such as man-made factors, the insufficiency of quality management in the printing process is also an important factor that causes the poor reproduction of image details. For this reason, this paper studies in detail the problem of poor reproduction of image layers due to insufficient tension.
The control of screen tension is an important aspect of improving screen printing quality. How can the tension of the four-color screen printing plate be consistent, and the effect of decreasing the plate tension on the printing quality is controlled to a minimum, and most screen printing is now The key issues that urgently need to be resolved. The relationship between the size of the plate tension and the mesh distance, the sufficient plate tension and the proper mesh distance, can make the substrate full of color, complete dot, and good image reproduction. This is because only when the plate has sufficient tension, the screen can overcome the ink viscosity to quickly separate the plate and the substrate. When the tension is insufficient, only increasing the distance can make the screen have enough tension to make the plate. Separation from the substrate. Assume that the plate tension is 10 N/cm and the mesh distance is 0.64 cm-2J. When the squeegee squeegees the screen, the squeegee pressure stretches the screen and the tension increases exponentially. At this time, the plate tension value is expected to reach 80N/cm, which can overcome the ink stickiness and quickly separate the printing plate and the substrate to ensure the accurate transmission of the dot size. For four-color overprinting, lON/cm is the lower limit that guarantees that printing can proceed smoothly. When the plate tension is insufficient, the screen plate cannot be separated from the substrate after the blade is scraped. The edge of the printed image is blurred, the ink overflows seriously, and the image quality cannot meet the customer's requirements.
l Printing failure due to insufficient plate tension
Tension relaxation phenomenon mainly has two kinds of situations: (1) The printing plate stretches the net not to be in place, the initial tension is insufficient; (2) After a large number of printings, the elasticity of the silk screen drops to cause the plate tension to be insufficient. In the former case, it is entirely possible to strictly follow the requirements on the printing worksheets during the stretching process. The latter situation is more complex. Different types of screens have different tension relaxations. How much tension is reduced to re-stretch the net, and how much the tension of the stretch net is controlled depends on various factors such as the type of mesh, specific work requirements, and characteristics of the print. Insufficient plate tension not only affects the print quality, but also reduces the work efficiency and increases the rejection rate. Printing operators often compensate for the lack of tension by increasing the spacing of the web to ensure rapid separation of the printing plate and the substrate. Although this can solve the problem of adhesion, it will also bring about some other printing problems.
1.1 Material waste and low productivity
In order to compensate for the lack of tension, the method of increasing the distance is often used. Due to the increase in the mesh distance, the printing plate can only come into contact with the substrate with a large squeegee pressure. Excessive scraping pressure leads to serious abrasion of the screen, which is particularly serious when the print volume is large. If an adjustable tension plate frame is used, the operator often needs to tighten the tension screw to increase the plate tension, affect the printing speed, and greatly reduce the printing efficiency. If non-adjustable tension plates are used, excessive scraping pressure reduces the use of screens, which not only slows down the printing speed but also causes material waste, which greatly increases printing costs.
1.2 Misregistration and image tilt
As mentioned above, the tension relaxation and the excessive mesh distance cause the screen plate to be stretched and deformed in the squeegee direction, and the pattern will be elongated longitudinally. And when multi-color printing often produces misprints, printing can not be positioned and other failures. When the screen tension is seriously insufficient, the screen will be displaced in the squeegee direction under the action of the squeegee (see Fig. 1). The printed image will be seriously distorted regardless of the gradation or sharpness.
1.3 Color deviation
Insufficient tension is used to increase the mesh distance to avoid adhesion of the printing plate and the substrate. Another print quality problem caused by this is color cast. If the net distance is large, the squeegee contact angle between the squeegee and the plate is small. The smaller the squeegee angle is, the more ink is squeezed by the squeegee across the screen. The increase in the amount of printing ink leads to enlargement of halftone dots, blurring of the edges of the image, and color shift of the image.
1.4 Scraper wear
The blank part of the screen plate is covered with a photosensitive layer and the surface is relatively smooth. However, the graphic part is composed of meshes that can leak ink and have a relatively rough surface. When the scraper forcefully squeegees on the screen, the rough surface has sandpaper-like properties, and the wear of the blade is inevitable. As we have discussed before, the relaxation of the tension of the printing plate eventually leads to a larger squeegee pressure during printing, and the larger squeegee pressure greatly accelerates the wear of the blade J. Judging the wear of the blade can be observed by the printed image, such as the edge is blurred, there is a phenomenon that shows the blade to replace the blade. And the situation of wear with different ink scrapers is also different. The author's experiments show that the uV ink wears more clearly on the blade.
2 plate tension control method
The above is the problems caused by the looseness of the printing plate tension. To ensure the plate tension and effectively control the tension drop is the key to avoid the above kinds of printing failures. The measures taken are mainly divided into two aspects.
2.1 Prepress Preparation
The first is to have a calibrated tension meter that is accurate. Tensiometers are instruments that measure tension in a stretch. The tension meter is used to sink the screen by its own weight, and the submerged value indicates the tension. The standard unit is N/cm. At least 5 points are to be measured during the measurement and the plate tension value is finally calculated. Tension meter test method can refer to screen printing and other publications will not repeat them here.
Second, through a number of experiments to determine a set of reasonable and accurate tension and network distance parameters table. In general, the higher the tension of the high-quality ED J~U product is, the better, and the smaller the mesh distance is, the better is the 0.3 cm. However, the tension of the stretch net is too large and the screen is easy to tear when printing. For the determination of screen tension, several factors must be considered. First of all, the type of wire mesh, the tension of the most commonly used metal-plated polyester mesh stretching meshes can be slightly larger, but less tension is required for poor quality polyester mesh meshes. Secondly, the best tension value is different for screens with different numbers of meshes. The greater the number of meshes, the greater the stretch tension should be. For example, the 180 mesh polyester web tension is controlled around 9.5 N/cm. Once again, the nature of printed images is different. Different stretch tensions should also be used. In general, such as printing a simple color block, the tension is not easy to be too large, but the printed line drawing graphic and halftone graphic text require a greater tension. Therefore, according to the specific circumstances, and through multiple production practices to ultimately determine the plate tension under different conditions. Moreover, the tension of the printing plate will gradually decrease during the printing process. When the tension of the plate drops to which force value, it is necessary to replace the screen or tighten the screen screw; when it is necessary to adjust the screw to increase the tension, it is also determined which The tension value is the most appropriate. These are questions that need to be studied slowly, not in one go. Therefore, if you want to get a reasonable and accurate reference table of tension and network distance, it must be a daily work.
First, the operator is required to record the tension value of each stretch net according to different meshes and types of screens, and then record the net pitch and screen printing resistance when printing. After several different production attempts, it is possible to obtain the most reasonable initial value of the tension and the initial distance of the screens according to the reference factors such as the printing quality and the printing resistance. For non-adjustable tension printing plates, as the number of printing increases, the screen tension will gradually decrease, and the operator can compensate for insufficient tension by gradually increasing the spacing of the screen. When the net distance increases to a certain value, the printing plate is scrapped when the printing quality cannot meet the customer's requirements. During the entire ED J~U process, the tension value and the net distance increase value and the final number of times of printing were recorded each time the net distance was increased, and a tension and net distance relationship reference table was established. For an adjustable tension plate, use the same method to record the value of each re-adjustment of the tension (in general, the re-adjustment of the tension value increases and is slightly greater than the initial tension value). In the end, a reference table for the relationship between the tension and the grid distance of different types of screen meshes and different mesh sizes can be established, which creates the necessary conditions for the continuity of high-quality printing.
2.2 Printing process
As a result of various preparations, control in the printing process is the key to ensuring accurate tension. The first is the choice of scraper and the determination of scraping pressure. Choosing the type and quality of the squeegee should take into account many different types of screen types, image characteristics and printing processes. For example, blade hardness, edge shape should be considered and selected according to the situation of different substrates. When printing on softer substrates such as fabrics, a harder blade is generally chosen. The harder material should choose a slightly smaller scraper.
After selecting the scraper, it is difficult to determine the reasonable pressure during the scraping process. Strictly speaking, the screen printing is pressureless printing, the printing plate does not exert pressure on the substrate, but the actual situation can not be achieved. Therefore, one of the principles to be adhered to is to use the most /J, squeegee pressure to print. When there is insufficient transfer ink, it is possible to increase the squeegee angle and appropriately increase the pressure of the ink return plate to increase the amount of ink added to the mesh in advance. If the effect is not obvious, you can use a smaller hardness scraper for printing. These measures can increase the amount of ink transfer. When it is determined that only the increase of the scratch pressure can solve the shortage of ink, a little bit of trial is also required. Because the excessive scraping pressure will not only cause some of the faults mentioned in this article, but also make the image produce pinholes and other printing failures.
Second, determine a reasonable distance. Experiments have shown that when the plate pressure is sufficient, the optimum spacing is 0.32 cm. Not only can you get high-quality prints but also can effectively extend the screen's printing life. But now the general printing manufacturers can not meet this requirement. The main reason for this has been discussed in the first half of this article.
Again, strengthen the management of training the operator's technical quality. Only by earnestly fulfilling the above requirements can we find the most reasonable set of process technology standards. The technical level of the operator is an important part of the impact of various measures. Enterprises should often carry out some technical training or skills competitions to improve the skills of skilled workers. Only in this way can the company ensure the stability of printing quality and make the improvement of the printing process into a virtuous circle.
Wang Qing, Lin Maohai
(Shandong Institute of Light Industry
Source: Packaging Engineering
There are many different styles of Brush Sets in this category. Some styles are normal, some are
special, and some are unique designed. Each set comes with both Face Brushes and Eye Brushes. In this category, you can find all the brushes that you may need for applying powder, blush, contour, highlighting, foundation, eye shadow, concealer, eyeliner, eyebrow, and lip products.
All the brushes are made with synthetic bristles which is cruelty-free, durable and easy to clean. Most of the brushes are made with aluminum ferrules which won't discolor or rust. A few of them are made with electroplated plastic ferrules which looks shinier. Handles of each brush are reasonably designed to fit your hand to hold.
Are you looking for a brush set? Just click into this category to have a look.
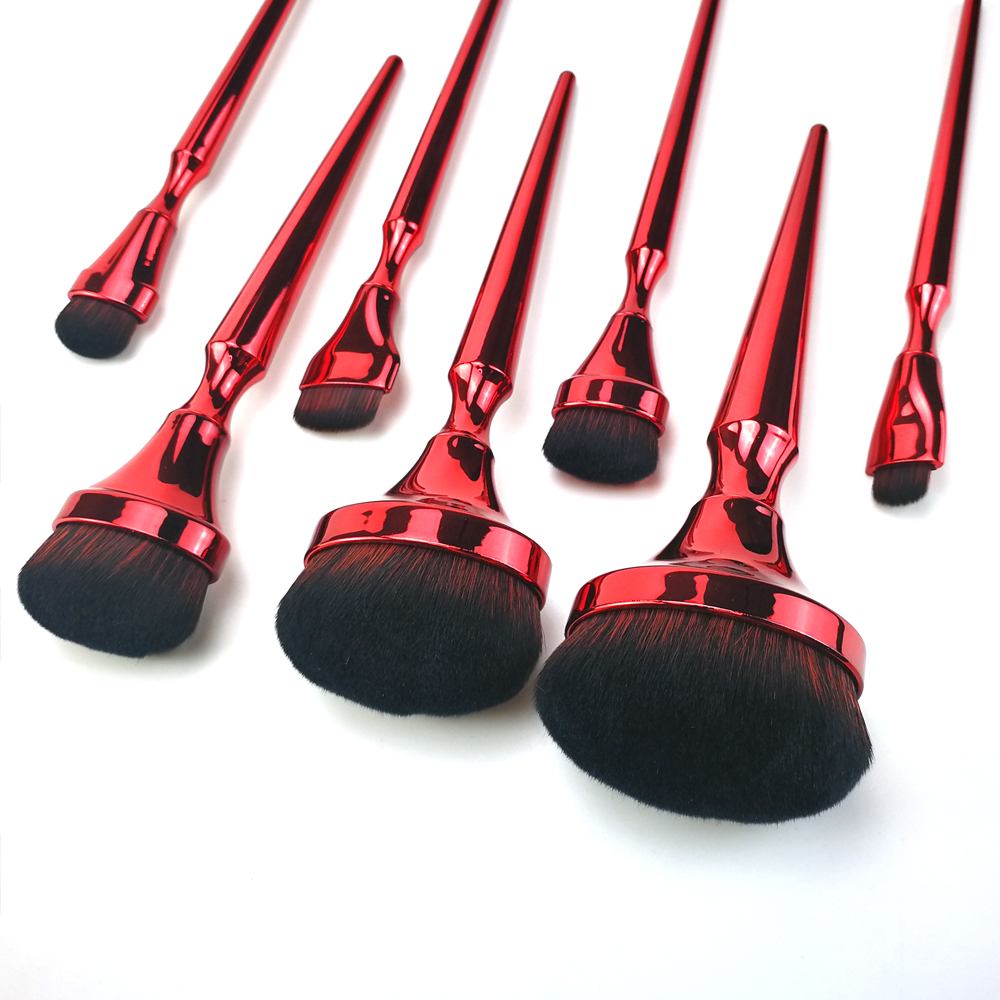
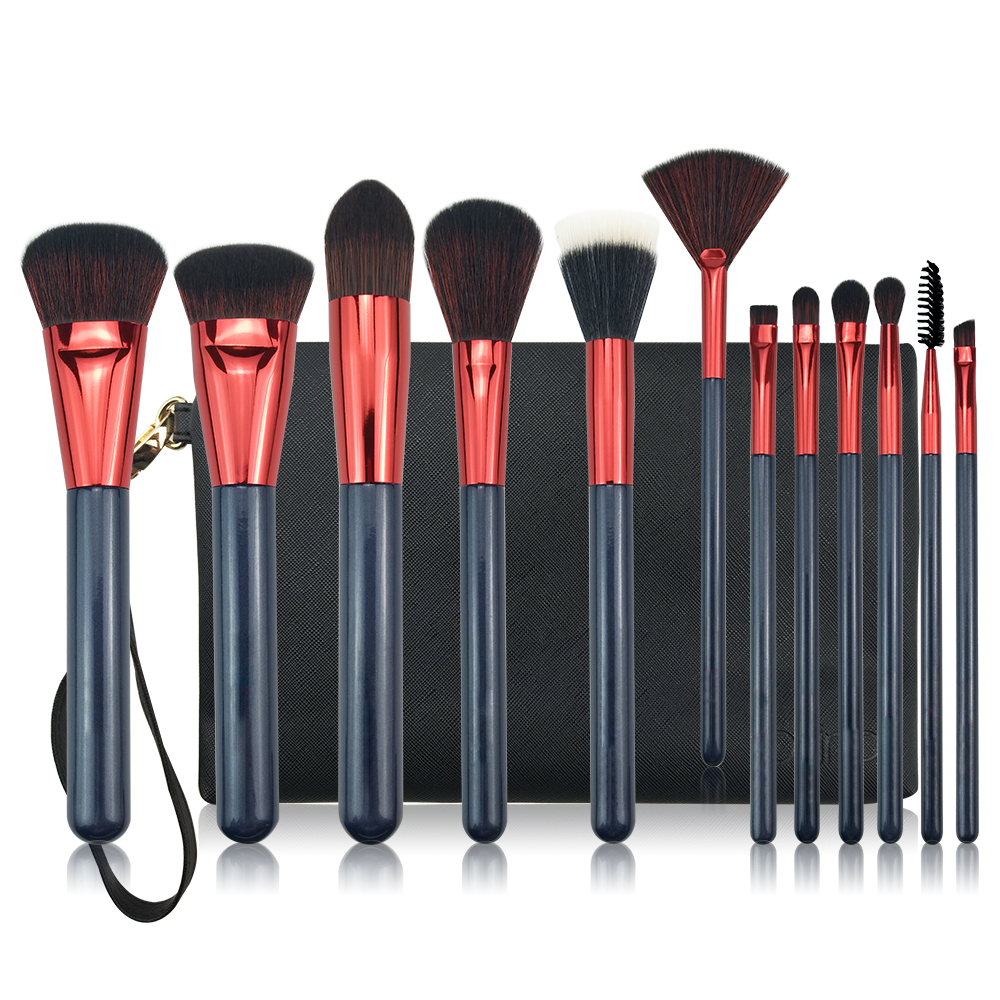
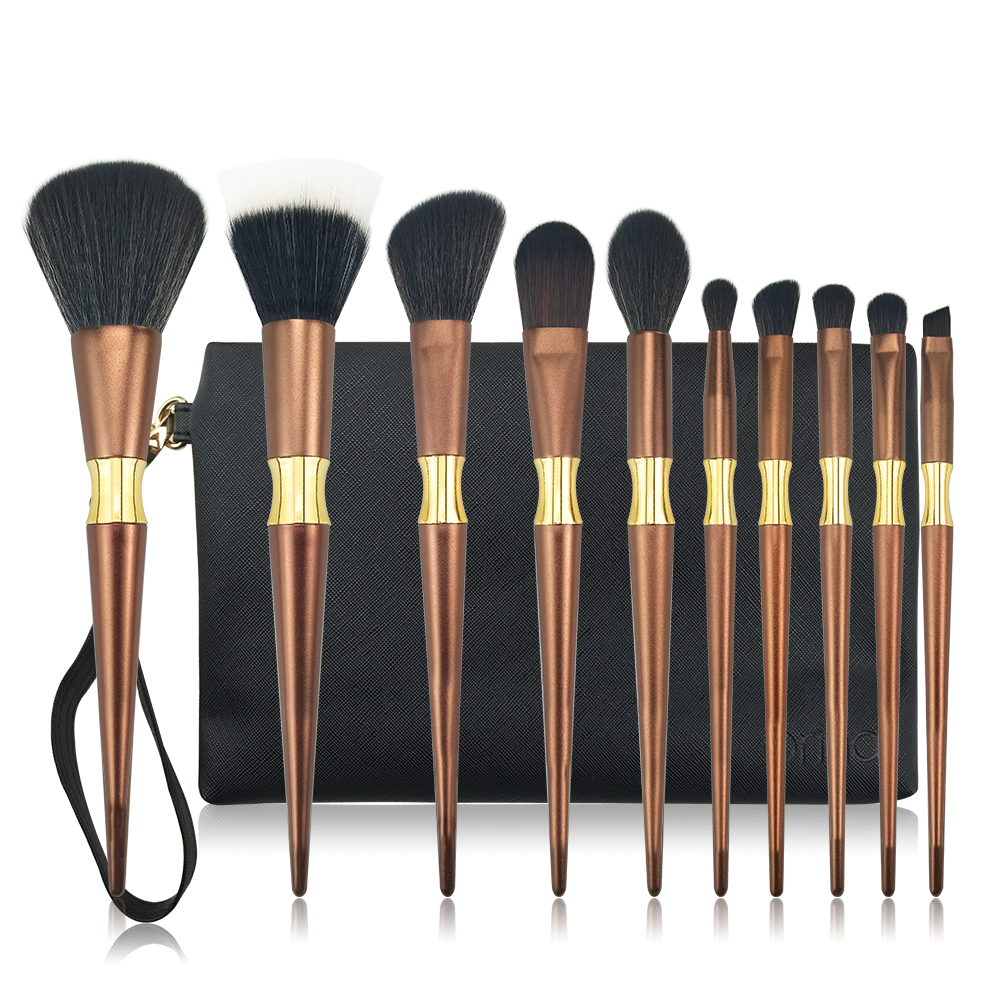
Brush Sets
Professional Makeup Brushes,Brush Sets,Flawless Brush Collection,Makeup Brush Set
SHENZHEN MERRYNICE COSMETICS CO., LTD , http://www.merrynice.com